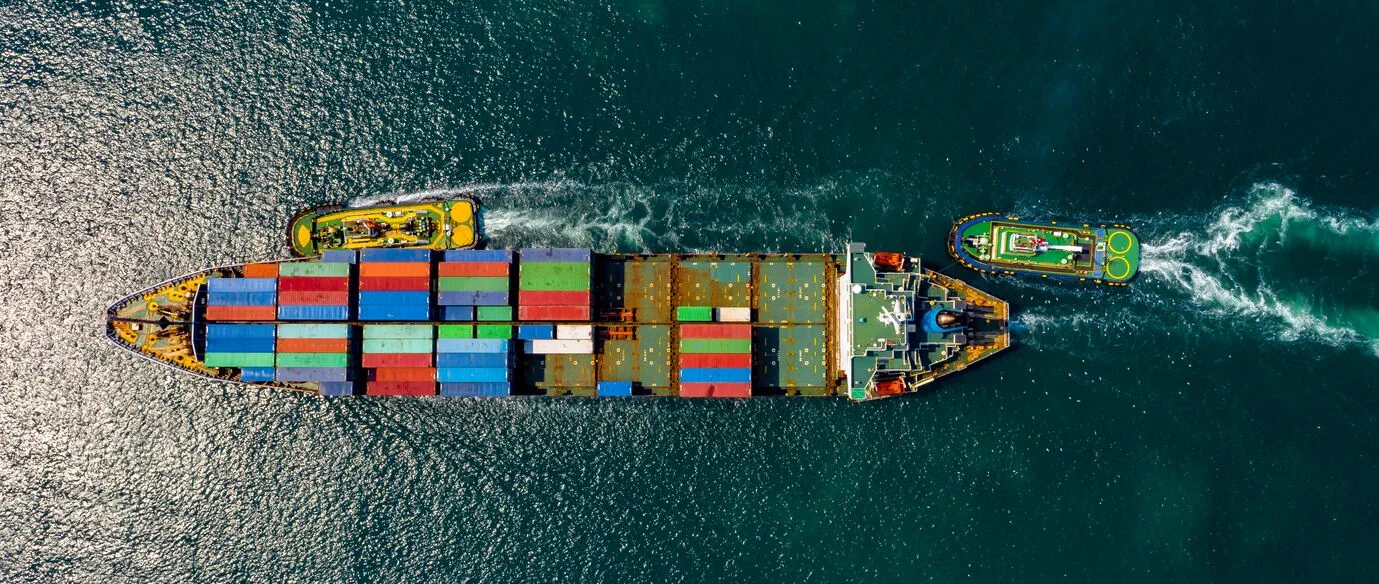
UK and U.S. economic prosperity deal takes effect – Key takeaways
The U.S. Food and Drug Administration (FDA) recently issued final guidance entitled “Conducting Remote Regulatory Assessments,” which explains the agency's plans to continue utilizing its records request authority and virtual inspection tools even after the COVID-19 public health emergency has ended. Taking into account the second Trump administration's stated priorities, we see that this guidance is yet another indicator that FDA is gearing up for more inspections and records requests for medical device manufacturing sites it deems critical to supply chain continuity and national security.
During the COVID-19 pandemic, with the vast majority of FDA’s inspectional activities on hold due to the public health emergency, FDA adapted and employed alternative oversight tools, including voluntary remote regulatory assessments (RRAs): a category that includes “remote interactive evaluations” and “remote record reviews.” For example, FDA increased use of sampling and analytical testing of products at the border, and greater information sharing from trusted foreign regulatory partners through mutual recognition agreements (MRAs), as we summarized at the time online here.
Based on experiences during the public health emergency, FDA has repeatedly said it recognized the value of voluntary RRAs, and concluded that they should be used for certain scenarios outside the current pandemic and for all types of FDA-regulated products. With this final guidance, FDA is clearly signaling that remote assessments are not merely a contingency tool but a permanent fixture in its regulatory arsenal.
In July 2022, FDA issued draft guidance explaining the agency’s expectations around which entities will be subject to RRAs moving forward, what information FDA may request as part of an RRA, and the consequences for an establishment that declines an RRA; we summarized that draft guidance online here.
In January 2024, FDA issued a revised draft version of the guidance, which it has now finalized, with minimal changes. Both versions of the guidance from the past two years spell out how an RRA may be used by FDA to, among other potential purposes:
One change between the latest draft and final versions of the guidance is that the 2025 final version provides further information surrounding how RRAs may be used more regularly to verify corrective actions following inspections, gather information that FDA officials require for reviews of firms’ pending applications, and “in gaining compliance insight when it was not practicable to inspect.” While not explicitly included in the final version, RRAs may also assist FDA in requesting and obtaining information from submission sponsors and their contract test facilities when submission data integrity concerns arise.
FDA also adds in the final version a statement about how the agency will inform companies at the start of contact if an RRA is mandatory or voluntary, and under what authority the request is made. The guidance’s clarification on the voluntary versus mandatory nature of RRAs is critical. While FDA asserts it will not take enforcement action solely for refusal to participate in a voluntary RRA, the subtext is clear: refusal may trigger a full inspection or impact the review of a pending marketing submission.
The final guidance further adds clarification that FDA has discretion to consolidate multiple records requests under a single Form FDA 4003 when reviewing multiple applications during pre-approval and pre-licensing inspection.
As we predicted, FDA plans to continue to use its records request authority and virtual inspection tools in addition to the agency’s traditional on-site activities to allow for more targeted on-site inspections. The new Trump administration’s heightened focus on security in the supply chain will likely mean enhanced scrutiny for manufacturers of critical devices, and who are the sole source a medical product.
FDA’s ability to conduct RRAs without the logistical burden of international travel means that foreign sites are no longer shielded by geography. Indeed, with the reduction in U.S. government staffing and recent efforts to streamline FDA, it is possible that the agency will expand use of the RRA program moving forward, particularly where travel is difficult, as a precursor to inspections, or as a follow-up to prior inspections to address effectiveness of corrections. Thus, despite reductions in staffing at FDA, increasing remote assessment may mean more inspections (both on-site and virtual) and more records requests for manufacturing sites critical to supply chain continuity — particularly those manufacturing sites critical to the supply chain that are located outside the U.S.
Additionally, as the QMSR replaces the legacy 21 CFR Part 820 and formally incorporates ISO 13485:2016 by reference, the timing for full compliance with the QMSR is expected by February 2, 2026, and aligns with FDA’s planned increased use to RRAs. RRAs could well be used to assess transition progress, especially for firms with a history of compliance issues, those manufacturing critical devices, and foreign manufacturers.
The emphasis on document control, traceability, and CAPA effectiveness in RRAs mirrors ISO 13485’s core principles. Facilities that maintain robust document management systems and digital readiness will be better positioned to navigate these assessments without disruption. This includes validated electronic document management systems and secure video conferencing capabilities. Companies should review and update SOPs related to FDA interactions, ensuring they include protocols for responding to RRAs, including data security, confidentiality, and chain-of-custody for electronic records.
With this guidance, as well as FDA’s May 6, 2025, press release regarding plans to increase unannounced foreign inspections, medical device sponsors and manufacturers — particularly those overseas — must continue to ensure that inspection readiness plans consider records requests and interactive evaluations in coordination with on-site inspections. Companies should begin to implement means to address FDA’s expectations around technological capabilities for RRAs and remote reviews.
Authored by Lina Kontos, Michael Heyl, Jodi Scott, and Randy Prebula.